How Does a Fire Truck Water Pump Work?
Fire trucks are integral to firefighting efforts, providing both a means of transportation and a powerful delivery system for water to combat fires. The water pump on a fire truck is one of its most critical components. It allows firefighters to pump massive volumes of water at high pressure, helping control and extinguish fires effectively. But how exactly does this powerful pump work, and what enables it to maintain such high performance? This article explores the mechanics, technology, and engineering behind fire truck water pumps.
1. The Role of the Fire Truck Water Pump
The primary purpose of a fire truck water pump is to deliver large quantities of water quickly and efficiently. This water may come from onboard storage tanks, a hydrant, or even natural water sources like lakes or rivers. A fire truck’s pump must be able to draw water in, pressurize it, and then propel it through hoses and out of nozzles to reach various distances, pressures, and spray patterns.
Fire trucks typically use centrifugal pumps because they are both powerful and efficient for the task. Centrifugal pumps rely on rotating impellers that rapidly increase the water pressure and move it to the point of discharge.

2. Key Components of a Fire Truck Pump
To understand how fire truck pumps work, it’s essential to familiarize ourselves with the main components involved:
– Impellers: These are spinning blades inside the pump that drive water outwards by centrifugal force. They spin at high speeds to push water toward the outer walls of the pump chamber, creating pressure.
– Pump Casing: This houses the impellers and directs the flow of water. The shape of the casing helps control the pressure and flow of the water.
– Intake Valves: These allow water to enter the pump from an external source, whether that’s the onboard tank, a hydrant, or another source.
– Discharge Valves: These valves control the flow of water leaving the pump and direct it through hoses toward the fire.
– Relief Valves: Safety devices that prevent the pump from exceeding certain pressure levels, helping avoid damage to the equipment.
– Primer System: Used to remove air from the pump system, which is critical when drawing water from natural sources, as air can interrupt the pump’s suction capabilities.
3. How Does the Pump Work? The Process Step-by-Step
The operation of a fire truck water pump involves several steps, from engaging the pump to delivering water at high pressures.
Step 1: Engaging the Pump
When firefighters arrive on the scene, they activate the pump by engaging a power take-off (PTO) from the fire truck’s engine. This transfers power from the truck’s engine to the pump, providing the energy needed for the impellers to start spinning. In most modern fire trucks, this engagement is done with a simple switch inside the cab or at the pump panel.
Step 2: Drawing Water In
The water pump either pulls water from an onboard tank or through an intake valve connected to a hydrant or other water source. If drawing from a hydrant, gravity often aids in the water’s flow, making it easier for the pump to pressurize the water.
For non-pressurized water sources, such as lakes or ponds, the primer system comes into play. By creating a vacuum, the primer removes air from the pump chamber, allowing atmospheric pressure to push water into the pump, ensuring a continuous supply.
Step 3: Pressurizing Water
The water moves through the pump casing to the impellers, where the pressurization happens. When the impellers rotate, they force water outward due to centrifugal force, creating high pressure. As the impellers continue spinning, they move the water towards the pump’s outer walls, where the flow velocity is reduced, but the pressure remains high.
Fire trucks are designed with either a single-stage or multi-stage centrifugal pump:
– Single-Stage Pumps: These have one impeller and are ideal for smaller fires or situations where ultra-high pressure isn’t necessary. They’re simpler and lighter, allowing easier maintenance.
– Multi-Stage Pumps: These pumps have 2 impellers, with the first impeller feeding into the second. This design boosts water pressure significantly, which is beneficial when fighting large fires or when long hose lengths are required.
Step 4: Directing the Water
The pressurized water moves from the impellers to the discharge valves. By opening and closing these valves, firefighters can control the amount and direction of water flow to specific hoses. Modern fire trucks often include a control panel that allows precise adjustments of pressure, flow rate, and discharge direction, optimizing the water output to match firefighting needs.
Step 5: Adjusting Flow and Pressure
For effective firefighting, water pressure must often be fine-tuned based on the situation. For instance, when water needs to be delivered over long distances or upwards, such as in tall buildings, higher pressures are necessary to overcome gravitational forces and friction loss in hoses. In other scenarios, lower pressure may be ideal to prevent damage or ensure safer operation.
Fire truck pumps are equipped with relief valves to automatically adjust the pressure when necessary. If the pump begins to over-pressurize, the relief valve opens, releasing water back to the intake side of the pump to stabilize pressure.
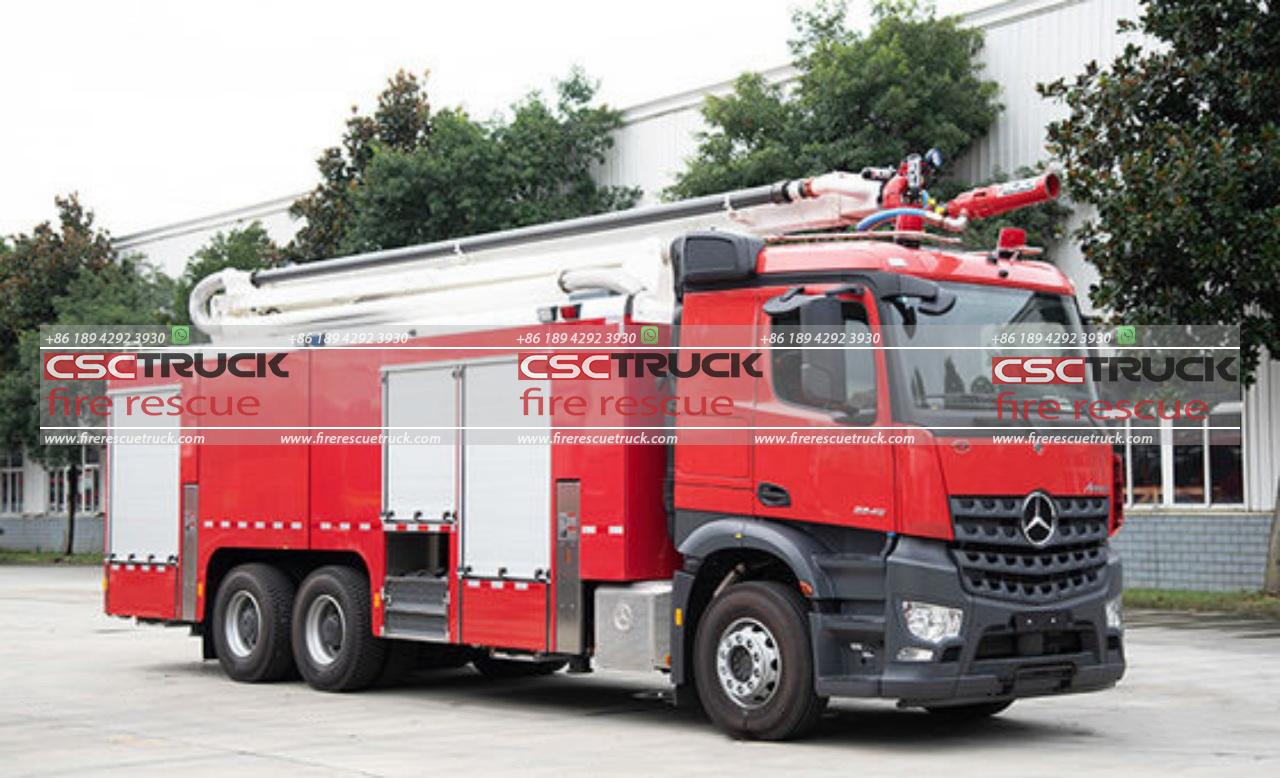
4. Maintaining the Pump: Ensuring Reliability
Given the critical role fire truck pumps play in emergencies, regular maintenance is essential. Some key aspects include:
– Lubrication of Moving Parts: Impellers, seals, and valves need regular lubrication to prevent wear.
– Inspection of Valves and Hoses: Ensuring no blockages, leaks, or wear points that might reduce efficiency or create hazards.
– Primer System Maintenance: Primers must be kept free from obstructions and tested to ensure that they can create adequate vacuum pressure when required.
– Testing and Drills: Regular operation checks help detect issues before they become critical and ensure firefighters are familiar with the equipment.
5. Technological Advancements in Fire Truck Pumps
Modern firefighting relies on advancements in technology to improve safety, efficiency, and effectiveness. New fire truck pumps often incorporate digital controls, allowing for real-time monitoring of water pressure, flow rate, and pump status. Some systems even offer remote operation capabilities, letting firefighters adjust pump settings without being physically at the panel.
Additionally, many newer pumps use advanced priming technologies that work more reliably under different environmental conditions, such as extreme temperatures or elevations. Improved impeller materials, such as corrosion-resistant alloys, also enhance the longevity and reliability of fire truck pumps, reducing maintenance needs and increasing performance.
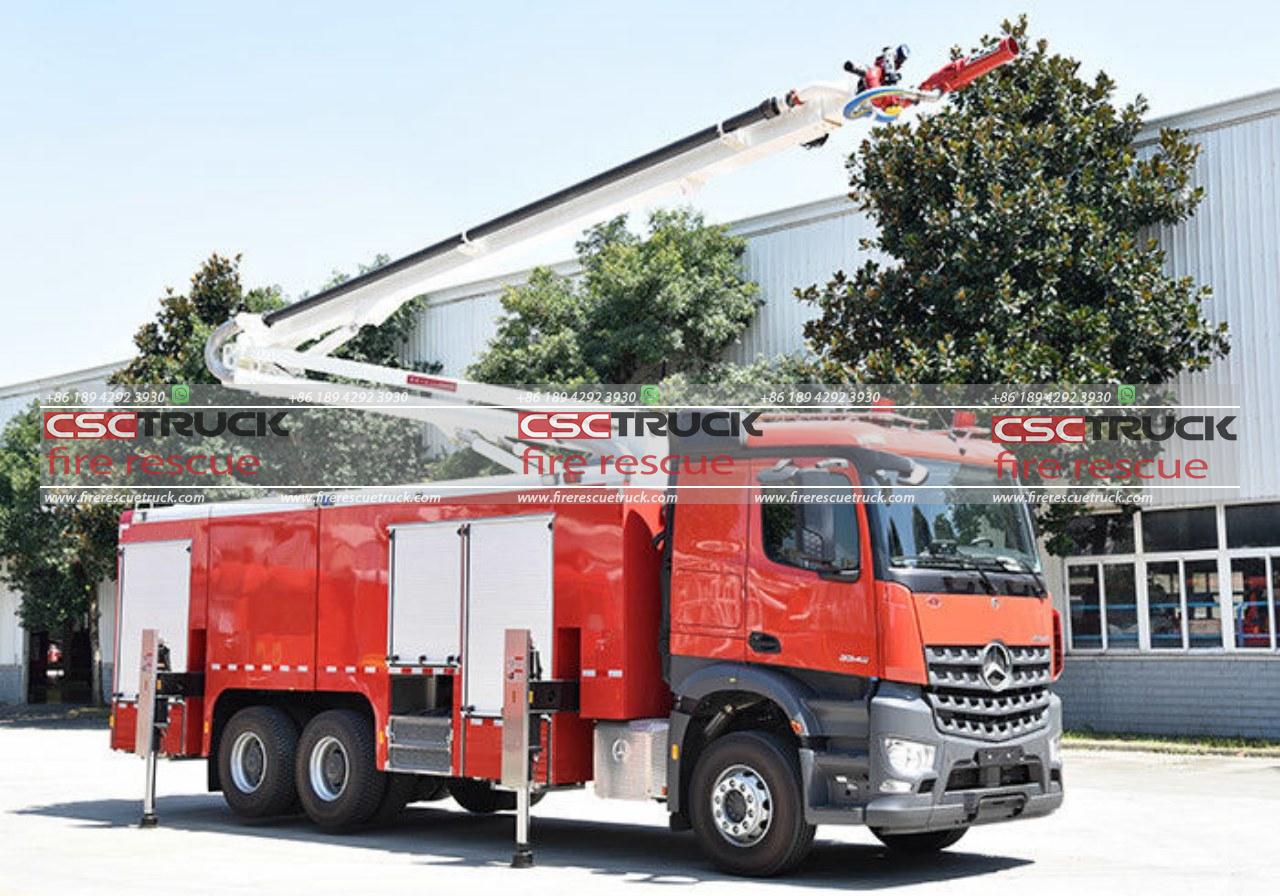
Conclusion
Fire truck water pumps are marvels of engineering, designed to be both powerful and reliable. By using centrifugal force, these pumps can generate immense pressure, making them ideal for firefighting applications. Understanding how they work not only provides insight into the complexity of firefighting equipment but also highlights the importance of regular maintenance, technological advancements, and skilled operation in making firefighting safer and more effective.
Ultimately, a fire truck’s water pump is a crucial part of every firefighting mission, providing firefighters with the tools they need to protect lives and property. The evolution of pump technology continues to advance firefighting capabilities, making it an exciting and vital area within the field of emergency services.